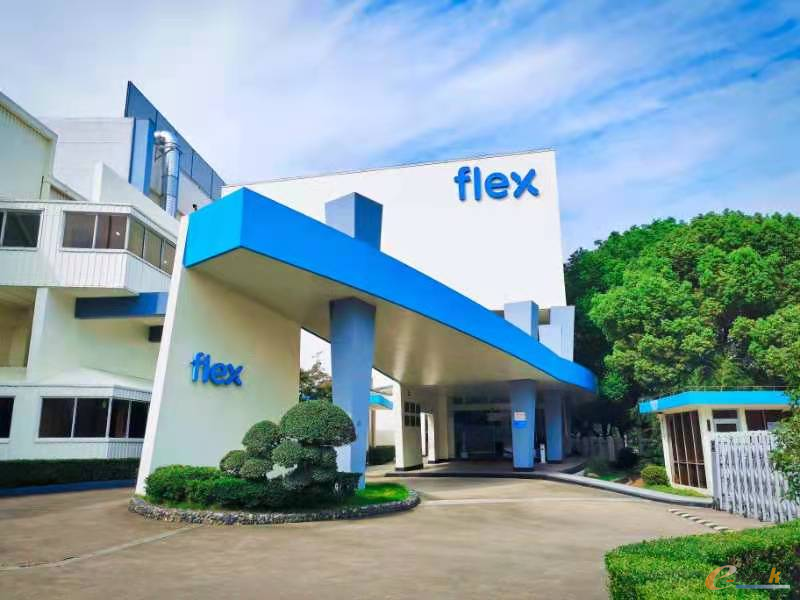
图1 伟创力电子技术(苏州)有限公司
二、企业在智能制造方面的现状
为加快企业互联网化提升建设,提高工作效率,降低成本,提升公司管理水平,公司实行了一系列互联网化提升建设。公司拥有千兆速率光纤接入通道,内部实现了5G无线和WIFI全覆盖。随着近几年信息化建设的大力发展,我公司基于企业资源计划(Enterprise Resources Planning,简称ERP)系统平台,对公司内部业务流程和管理过程进行优化,并在此基础上,成功导入PDM,将最终研发成果与ERP系统无缝对接,顺利完成跨部门平行工作的开展。通过文件管理系统,实现了无纸化办公,为推动绿色环保做出贡献。通过历年来的信息化持续创新投入和提升,实现了企业内外部的高效协同互联,提高了公司的经济效益和市场竞争力。
公司一直非常重视研发费用的投入,自2003年以来公司完善研发模式、研发机构及研发体制,每年的研发费用均超过公司总营收的3%以上。建立了比较完善的研发激励制度。同时为了保障公司研发团队的稳定及核心产品技术的自主知识产权,与所有研发人员均签署了保密协议,与核心技术人员在双方自愿的基础上签订了中长期劳动合同。
伟创力电子技术(苏州)有限公司是全球领先的电子产品制造服务供应商(EMS),专注于为汽车制造业、电脑制造业、数码电子消费品制造业、工业、电信业基础设施、医疗器械制造业及移动通信产品制造业内的OEMS(原始设备生产商)提供集设计、工程与制造于一体的一站式服务,常年国际排名第二名。公司还获得TL9000通讯电子质量管理体系、IATF16949汽车行业质量管理体系、ISO13485医疗器械质量管理体系、ISO27001信息安全认证、AS9100航空航天质量管理体系等体系认证,具备行业技术服务领先优势。
公司一直以客户价值为中心来培育公司的核心能力——技术创新。为此,公司密切追踪最新技术应用及市场、技术发展趋势,持续展开对新产品以及新业务的可行性研究;加强对技术人才的引进和提升、加大研发投入、创造优良的技术开发环境、建设创新机制;在自主创新的基础上,积极展开与科研院校、研究机构等的技术合作;规范研发管理,缩短新产品开发周期,使公司在市场竞争中具备技术和产品储备优势。
三、参评智能制造项目详细情况介绍
1. 项目背景介绍
由于难以考虑到复杂的资源约束、实际加工工时的不确定性、任务的不确定性、手工计划方式的随意性,现场制造计划难有效制定和管理;制造现场靠人工方式打印下发生产指令,车间基本靠人为控制,在各种计划变更、追加计划、设计变更,现场突发事件等的冲击下,人工管理无法及时进行合理的反应,并安排出最有效的制造计划。存在如下问题:
1)现场信息反馈不及时,计划无法跟踪
2)设备利用率、稼动率、设备维修及费用等问题
目前均为人工保修,流程繁琐,效率不高,并且无法准确掌握每台设备的使用情况,维护情况,维修费用,经常会有哪些零件造成保修。
3)生产进度、工时等信息统计,生产物料核对问题
生物管每天需要花费大量时间用在与组装,机加核对物料进度上,目前基本用Excel统计,核对,其准确度,效率低下,MES二期报表将解决此类问题。
4)质量管理数据报表均为手工统计
质量是生产出来的,不是检验出来的。现场实时生产大量成品半成品,靠人工及时发现所有的质量问题是不可能的。由于缺乏先进的手段,对生产过程中的质量数据没有及时的采集和保存,各级质量标准中的大量质量控制参数往往根据经验制定,缺乏科学的定量分析。需要运用现代化的工具,采集生产过程的质量数据,进行科学的定量分析,使质量控制参数的制定科学严谨、更趋精确。目前现场质量数据基本通过纸质文档记录,事后录入,而且对维修过程的管理相对比较薄弱,基本没有数据供后期追溯和分析。质量数据没有自动采集的手段,大量依靠手工方式记录,这种质量数据只能用做备查,而无法为系统所分析利用,无法形成长期的质量监控分析报表,不利于发现问题,解决质量波动等问题,难以支撑长期质量的提升。
5)现场制造可视化程度低
目前的整个生产状态,计划执行情况、质量情况、物流情况、产线运行情况、各种异常信息等,主管部门和相关领导都无法进行实时有效的监控和管理,也就无法做到及时决策,造成了下面的问题无法及时反馈,上层的意图无法及时贯彻,各种突发问题处理不及时的情况;
6)信息无法高效传递
各应用系统相对独立,各有对应的上级、下级业务关系,无形中增加了不必要的业务环节和业务量,造成资金、人力浪费,并使横向的跨部门的信息不能共享。部门之间需协调的因素复杂,沟通难度加大,使得局部目标与全局目标的偏差加大,阻碍了跨部门业务流程的顺利进行,多层次的组织结构和层层汇报无法实现信息的快速传递,使得效率难以提高。
2. 项目实施与应用情况详细介绍
1)通过双轨闭环式全流程自动化生产线技术改造,实现了通讯互联设备双面制作的柔性化高效生产,更换产品实现不停机,利用视觉图像识别技术,可区分产品正反面及产品类别,利用空中回型轨道可将产品送回线头,实现单机复式双面加工生产。有效降低车间占地面积需求,提高了单位面积产值。
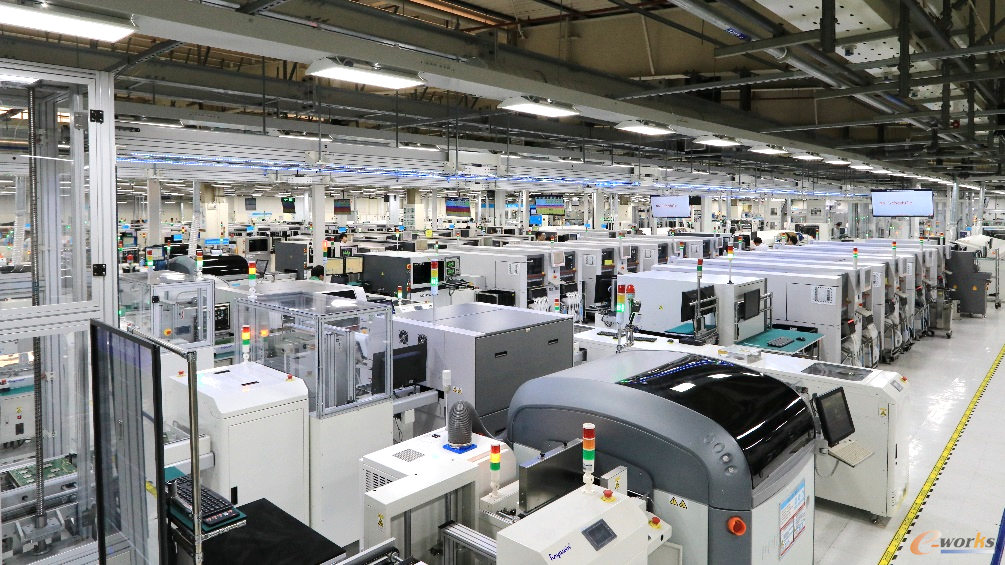
图2 高效双轨闭环式生产线实物图
2)自主开发了全厂智能运营管理系统,改变传统管理模式,真正实现数字化管理,数字化控制,数字化沟通,以及最终通过大数据分析的及预测的数字化决策。基于伟创力生产执行系统(FlexFlow)以及产线设备数据,对数据进行自动筛选,上传及智能分析,开发可以通过网络直接搜集数据并进行分类统计的显示系统。此系统集数据采集,筛选,分析,显示,查询于一体,并可以实现信息的上传,涵盖产线效率实时看板、设备产能分析系统、设备效率和利用率分析系统、全段质量分析系统、改善方案跟踪系统、测试检测分析系统、板子维修系统等等,极大地缩短了产线数据分析的时间,提高了产线的运营效率,并降低了产品的质量风险。

图3 全厂运营管理系统示意图
3)智能化排产系统(Random Group Setup),实现了多订单与生产实时状况的匹配优化,可实现生产计划的动态优化调整,显著提升了生产效率。根据物料计划以及客户订单交付等相关的优先顺序生成的初步生产计划,再按照产品生产流程工序、产能、瓶颈工位、人员等限制条件优化调整排程方案,生成最终的生产计划。每个班次结束后,根据flex flow 实时反馈的实际生产情况,或新增加的工单进行动态优化调整,系统在考虑客户订单交付日期的情况下,可生成新的排程计划。该系统可以通过看板及进程图及时跟踪生产计划完成情况以及各生产线的计划完成率,诸如生产工序甘特图,每条产线资源占用图等采用智能化的软件,可以根据客户的订单需求(小批量多品种)生成与之匹配的生产程序,系统自动会比对产品资料表的信息,确保生产程序的准确性。
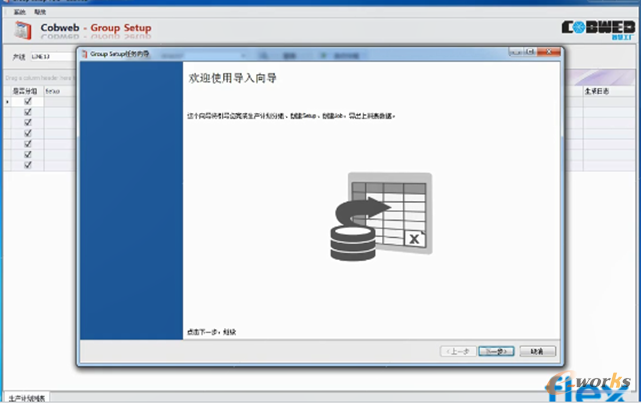
图4 智能化排产系统示意图
4)设备联网情况介绍
通过星型架构通讯控制方式实现了车间所有自动化设备的联网管理,车间生产设备联网数为133台,占自动化设备总量比例为100%。
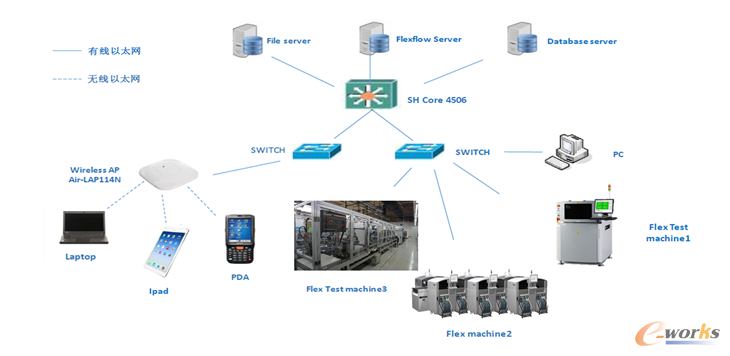
图5 车间信息网络结构图
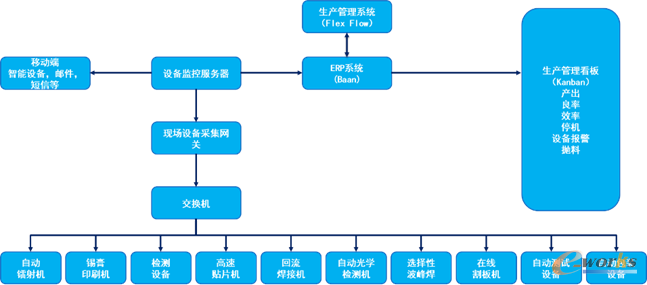
图6 车间信息通信系统结构图
整个车间信息联网控制系统内容包括:各设备的系统工艺参数的监测及设置,各运行数据的采集、处理及管控。具体架构说明如下:
(1)设备监测:对锡膏印刷机、检测设备、高速贴片机、回流焊接机、自动光学检测机、选择性波峰焊机、自动测试设备、自动包装等设备信息进行采集。
(2)设备控制:对各设备控制回路按生产流程实施优化闭环控制,根据设备当前的运行状况调整相关其他配套设备,优化设备生产工艺参数。
(3)设备故障报警及处理:车间各个设备的运行状态实时与系统监控端通信并展示产出和良率情况。自动化的装配和测试设备发生任何故障时,会自动停机,信号灯跳红,操作屏幕显示故障代码、相关错误描述以及特殊情况下的推荐处理措施。
(4)生产数据可视化:对生产过程关键参数、每班生产状况进行历史数据存储及数据分析,为生产管理提供现场的实时数据。针对生产中物料的使用情况,实时抓取物料的消耗,剩余数量已经可用的板子数量,指导员工及时的续料。提升设备的效率。
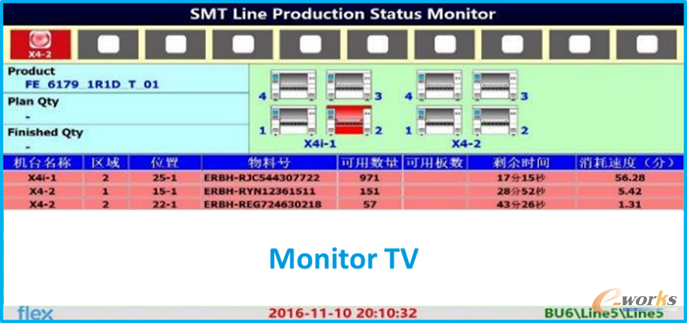
图7 设备联网数据可视化示意图
5)生产过程实时调度
生产设备运行状态实时监控、故障报警和远程诊断分析情况,生产任务指挥调度、车间作业计划生成情况,生产制造过程中物料投放、产品产出数据采集传送情况,生产制造过程根据计划、物料、设备等数据变化和异常自动动态调度情况。请提供制造执行系统的架构,描述与生产直接相关的子系统的功能;描述制造执行系统(MES)与企业资源计划管理系统(ERP)集成的技术方案。
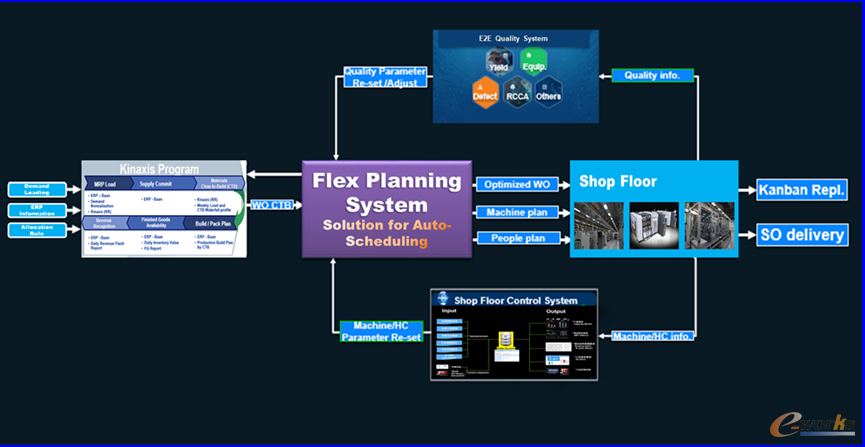
图8 制造执行系统架构图
6)生产计划实时调度系统(EPPS)
通过与MPS计划与机器同时连接的方式,实现了对生产进程的实时监控,可对生产计划进行动态调整优化。
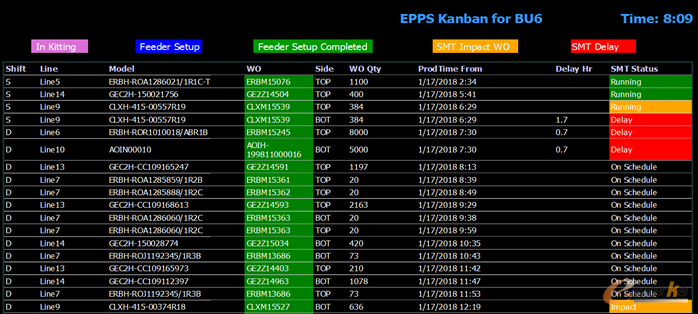
图9 生产计划实时调度系统(EPPS)
7)生产设备运行实时监控系统
采用无线射频技术采集设备的报警信息,车间各个设备的运行状态实时与系统监控端通信并展示出来,采用移动智能设备将报警信息通知技术人员和管理人员,以确保问题得到早期关注和处理,并可建立设备运行档案,提高设备测试良率。
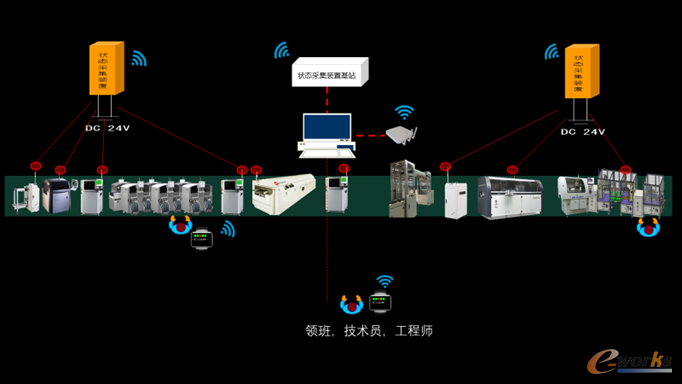
图10 无线射频报警系统
8)产品质量实时监控中心(Remote Control)
通过远程控制多台设备,将各个设备检测的缺陷信息和图像按照生产需求优先级的方式显示在控制终端,员工在控制终端可以判断所有被测试板子的缺陷信息,同时该系统根据AOI(自动光学检测机)的检测结果,自动调用相关的IPC判断标准、历史缺陷图片和需要重点检验元件的图片,供操作员参考判断现有的报警信息。
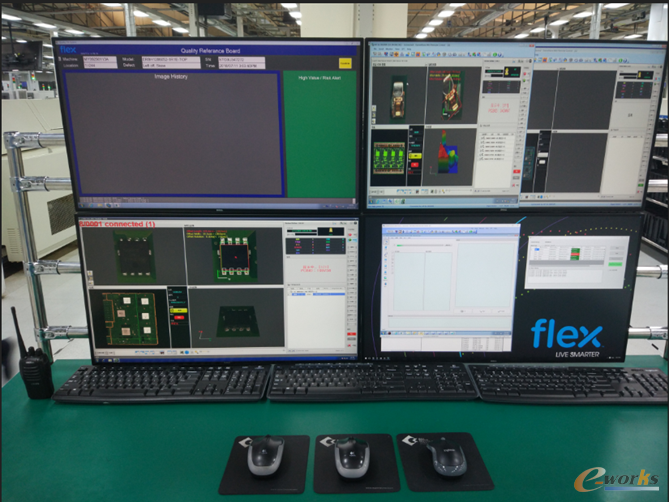
图11 远程监控中心
9)IEDB- Industrial Engineering Database System 工艺数据系统
建立IE 标准化系统,标准化IE 相关参数设定,规范计算逻辑,制程命名分类等,取代各类不同格式的手工/excel表格,建立IE集成数据库。关联其他系统自动产生各类IE 相关的报表:IE 基本数据报表,设备和人员产能报表(capacity report)效率报表(表面贴装 OEE/LU, Efficiency),路由报表等(Routing report)。并作为input系统支持其他系统比如自动生产排程系统,Baan系统等。实现数据信息实时分享,提升工作效率,降低成本,支持公司系统集成化。
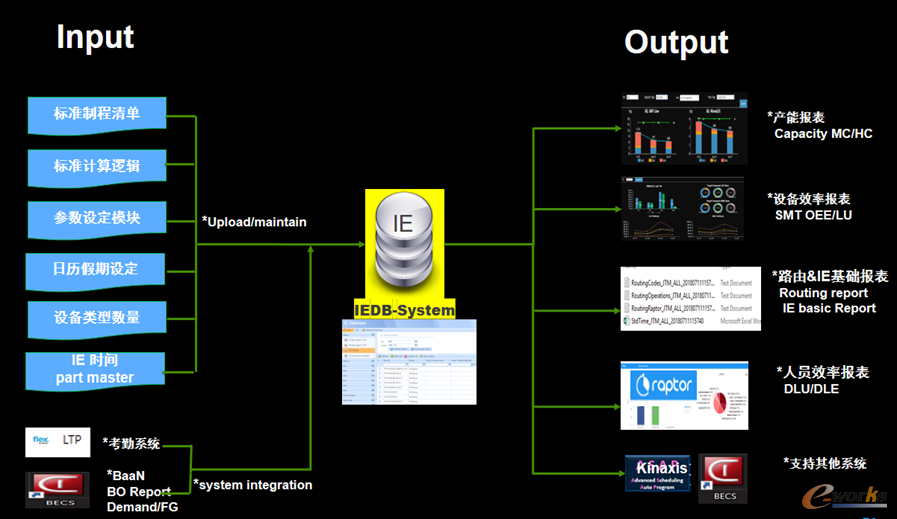
图12 IEDB 系统功能示意图
10)端对端产品质量分析监控系统
系统通过设置质量标准,对生产产品、生产流程的过程质量进行监控;可根据采集生产详细数据,生成生产状况的详细报表,绘制相应的各种统计图统计表,对生产过程质量和产品质量进行分析和监控管理。
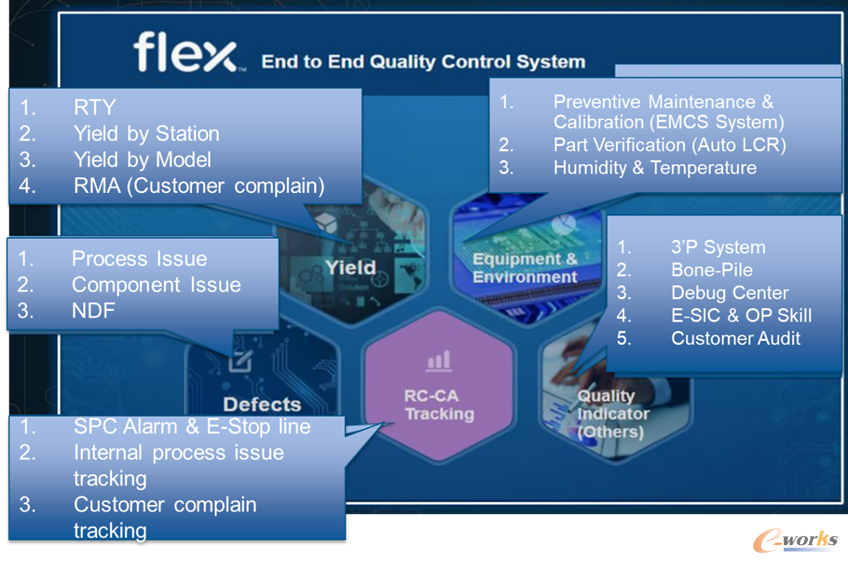
图13 端对端产品质量分析监控系统功能示意图
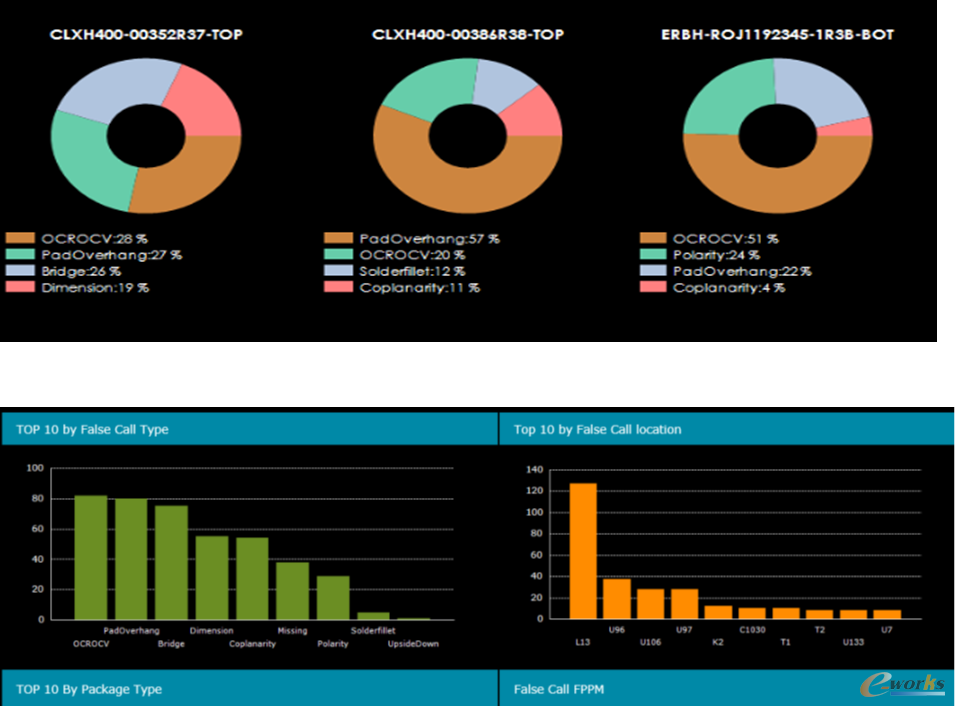
图14 端对端产品质量分析监控系统-生产质量统计报表
11)物料配送自动化
生产过程采用二维码、条形码、电子标签、移动扫描终端等自动识别技术设施的情况。请提供物流信息化系统的整体架构图;物流设施及设备的清单;描述物流系统的自动化、柔性化和网络化特征。请描述电子单证、无线射频识别等物联网技术的应用情况。请提供物流信息链软硬件系统架构图、信息集成图;描述多种运输方式的联动方式及效果;提供物流过程可视化、可追溯管理的实施方案;描述定制化增值服务的类别和相应的实施方案。
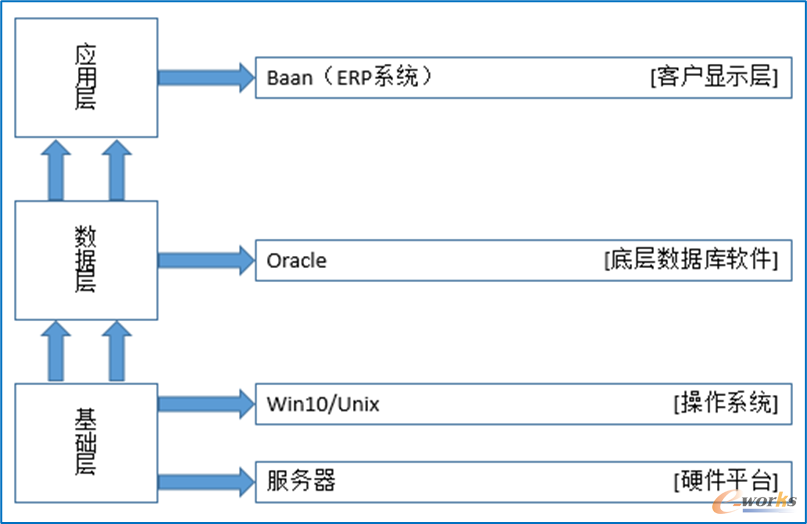
图15 物流信息化系统架构图
12)产品信息可追溯
在关键工序采用智能化质量检测设备情况,产品质量在线自动检测、自动记录及报警情况,产品质量信息实时上传信息系统情况。在原辅料供应、生产管理、仓储物流等环节采用智能化技术设备实时记录产品信息情况。通过产品档案对每个批次产品进行生产过程和使用物料的追溯情况。应用数据挖掘、性能监控、物联网智能终端等技术设备情况,对产品运行状态远程监控、远程诊断和故障自动分析处理情况。
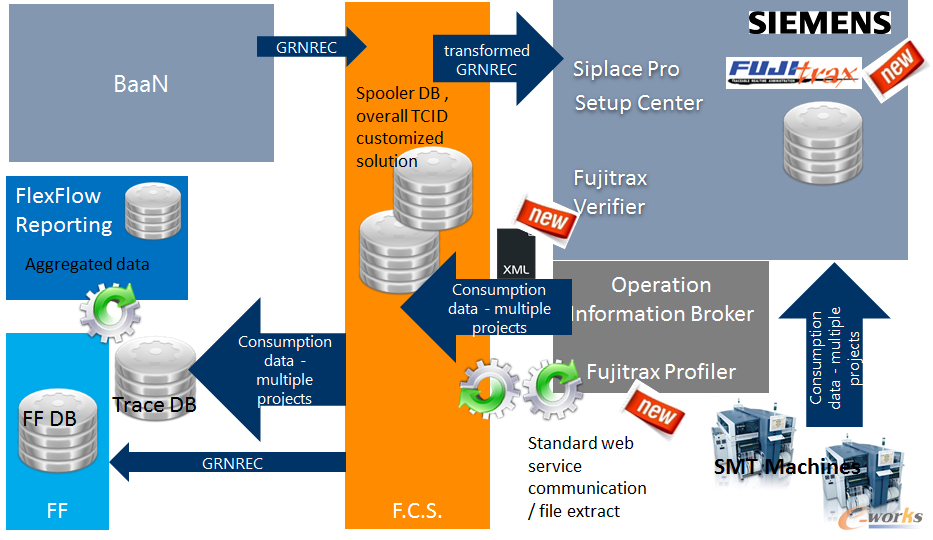
图16 产品追溯系统架构图
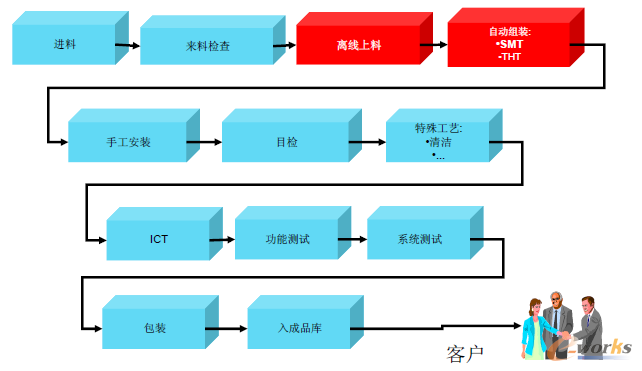
图17 产品信息全流程追溯示意图
13)关键工序采用智能化质量检测设备情况、产品质量在线自动检测、自动记录及报警情况
13.1、线路板外观在线自动检查系统:主要针对生产的线路板进行图像采集,对线路板上的料区的获取,对图像的亮度、灰阶变化、色差对比等进行分析对比,抓取损坏的料,进行区域提示;将检查的结果图片实时保存。
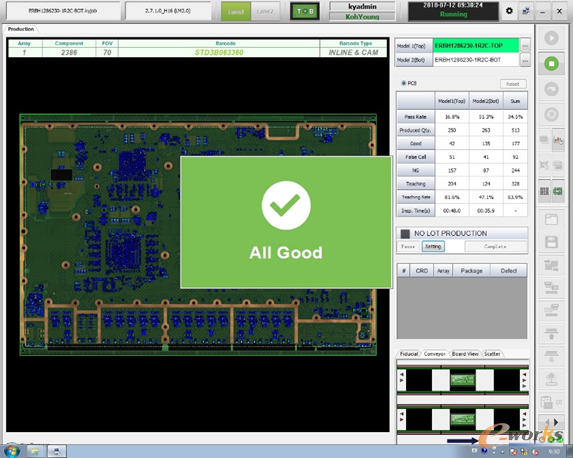
图18 成品电路板外观在线自动检查系统图
13.2、表面贴装产品质量在线实时监控系统:通过读取Flex Flow中生产过程中车间表面贴装生产线及工序的生产进度,实现对PCBA板生产的各工序的进度以及设备与模具等的状态的数据采集,并把生产过程中的进度信息及设备状态信息,通过车间LED大屏幕以及管理者办公室的液晶电视等设施,进行可视化动态展示。实现生产状态的透明化管理与可视化展示。提高生产过程中的快速响应处理能力。主要展现的内容如下:批次生产计划在各工序生产的实际进度或产量、各工序合格率、不良品数量以及类别、设备资源负荷状态、产线缺料状态、生产问题预警、质量问题预警等信息。
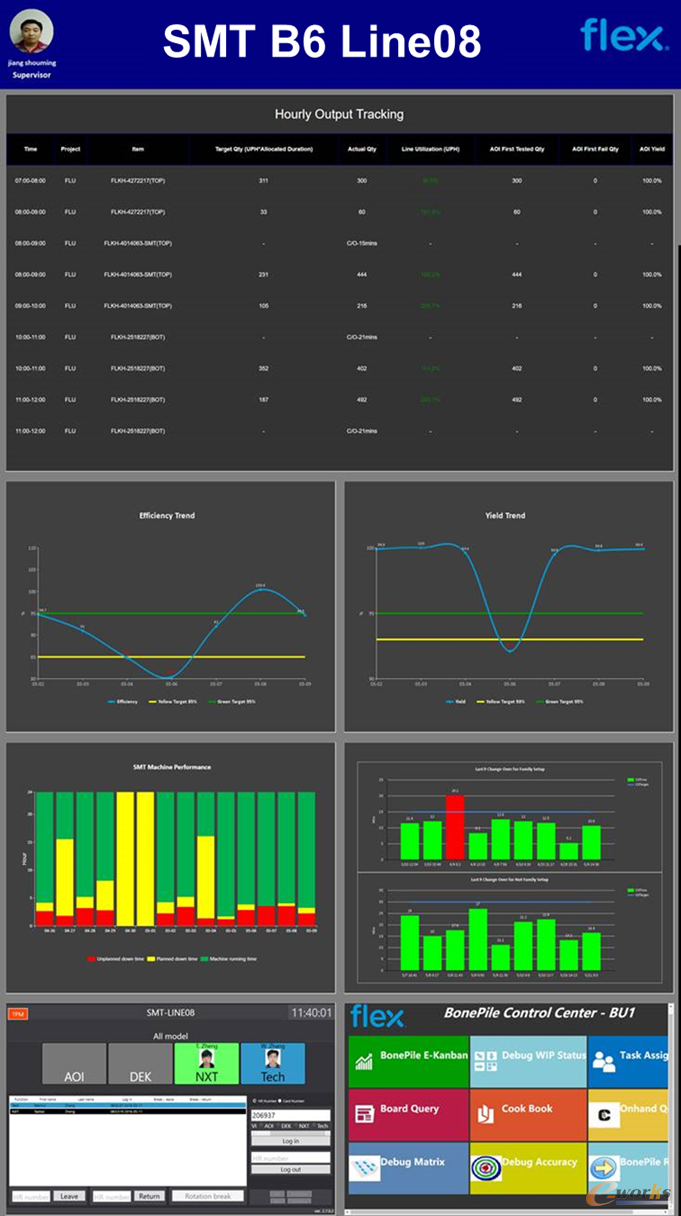
图19 表面贴装产品质量在线实时监控系统操作界面图
13.3、产品组装质量管控系统:产品组装计时跟踪,站别良率分析/每日良率分析等功能。
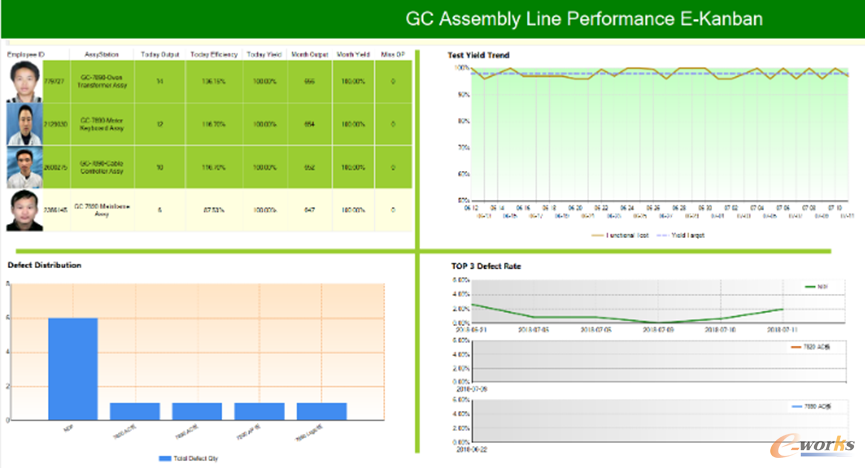
图20 产品组装质量管控系统操作界面图
13.4、PCBA测试机台智能监控系统:利用自动化测试线的状态跟踪系统,工程技术员及生产管理人员可以实时跟踪测试线的效率,每小时的产出,测试的良率,以及每片测试产品的测试信息。通过这些信息,可以判断实时判断自动化线的运行状态,任何异常可以提前预警,通知工程人员维护。
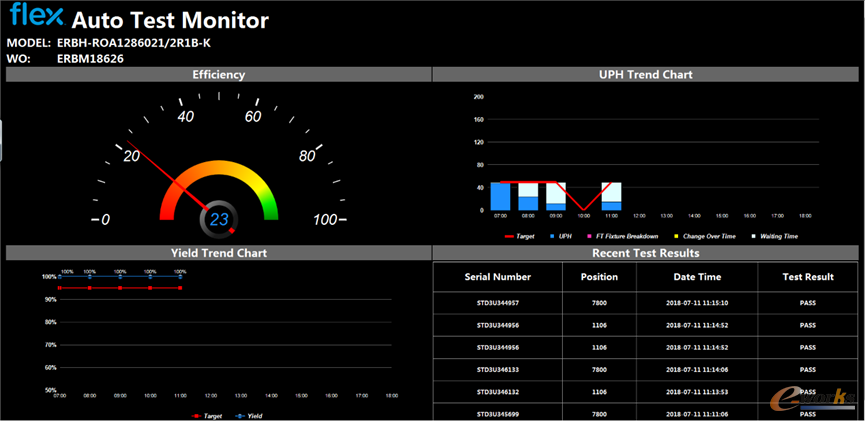
图21 PCBA测试机台智能监控系统操作界面图
13.5、产品质量信息实时上传信息系统情况,生产实时管理晴雨表软件:本软件基于目前伟创力生产线系统(Flex Flow),对数据进行智能分析,开发可以通过网络直接搜集数据并进行分类统计的晴雨表显示系统。实现以下功能:自动统计现有的各站位完成及未完成的产品的情况,并以晴雨表的方式大屏幕显示,对于历史数据,还可图表化显示;根据已经定义的报警时数进行报警显示;对于处于报警的产品,将会自动发送电子邮件给相关人员,以确保问题得到早期关注和处理,并可建立设备运行档案,提高设备测试良率。

图22 生产实时管理晴雨表软件系统界面图
14)智能设备保养管理系统
将纸质的保养单转换成电子表单,用户通过平板电脑,输入待保养机器的序列号,或扫描相应的二维码调取对应的保养单,根据保养单的检查项逐一完成各项保养,并将保养数值保存到系统中。工程师和质量控制部门通过本系统完成保养单核对和审批工作。保养完成后,用户通过便携式无线打印机自动打印出保养标签。质量控制部门在审核机器的保养记录时,可以通过本系统迅速检索到机器的保养。
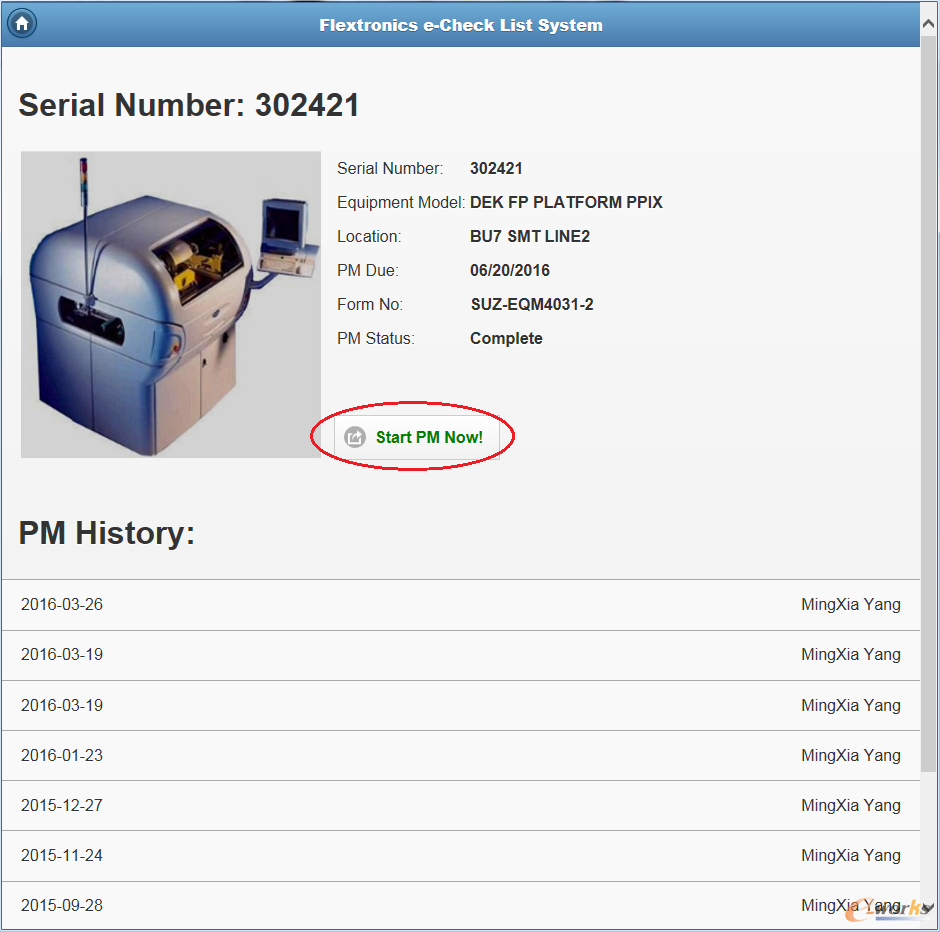
图23 智能设备保养管理系统操作界面图
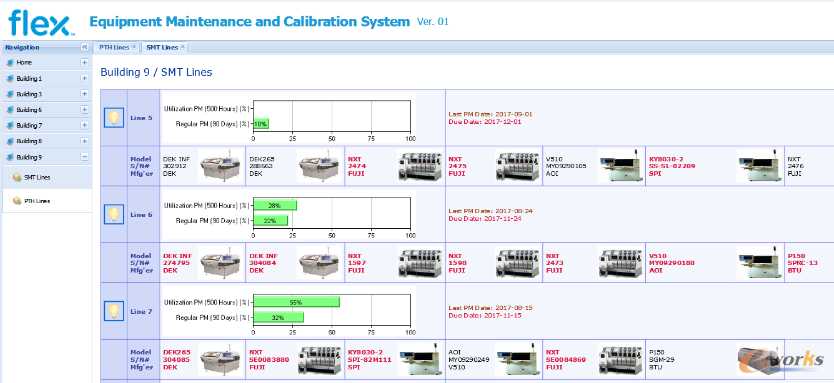
图24 智能设备保养管理系统操作界面图
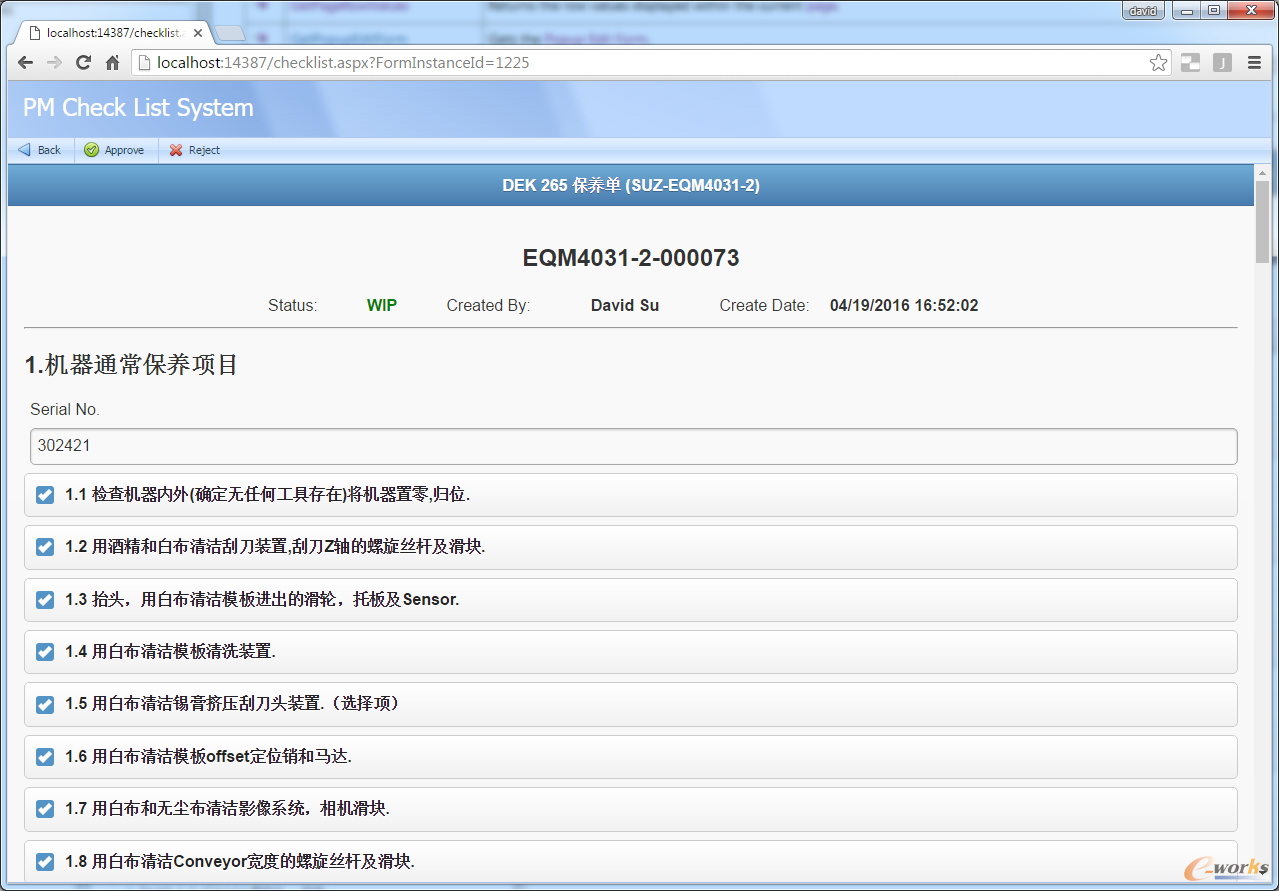
图25 智能设备保养管理系统操作界面图
15)MHDIOS/PVS备料系统:采用SKID物料唯一识别码,将物料的料号,数量,制造厂家,生产批次等信息集成在一个号码内,通过可视化的系统,实时显示物料的进出,消耗等情况,系统自动调度物料。
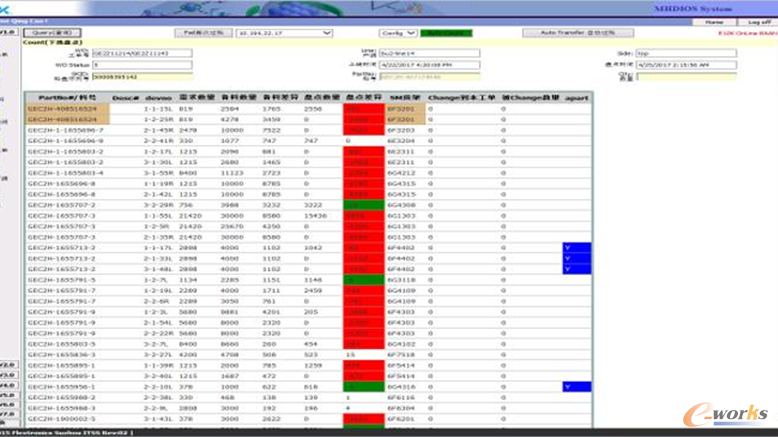
图26 MHDIOS备料系统
16)防错件系统:通过防错件系统,可以保证物料使用的准确性。通过扫描物料的唯一识别码,获取物料的信息后传回服务器进行与当前产品要求的物料信息比对。
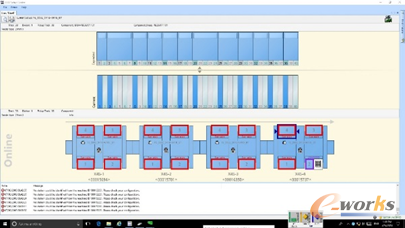
图27 防错件系统使用示意图
17)PCB自动扫描系统:通过安装的自动扫描枪,自动记录每块板子的条码信息,并传给服务器进行保存。
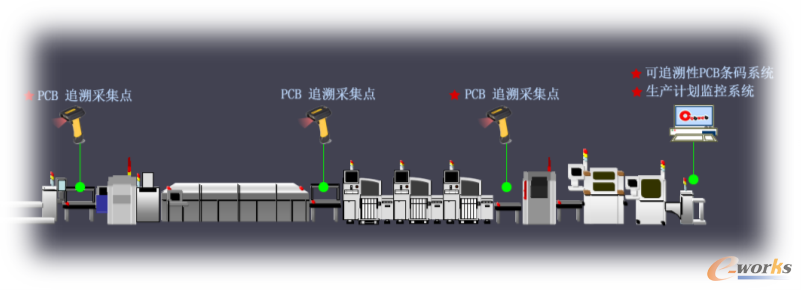
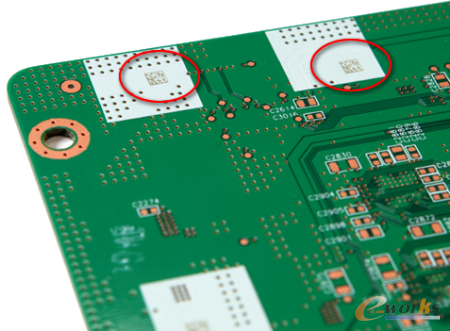
图28、29 PCB自动扫描系统示意图
18)AR虚拟远程诊断:通过AR眼镜实现远程操作知道,远程诊断产品质量,设备故障等。
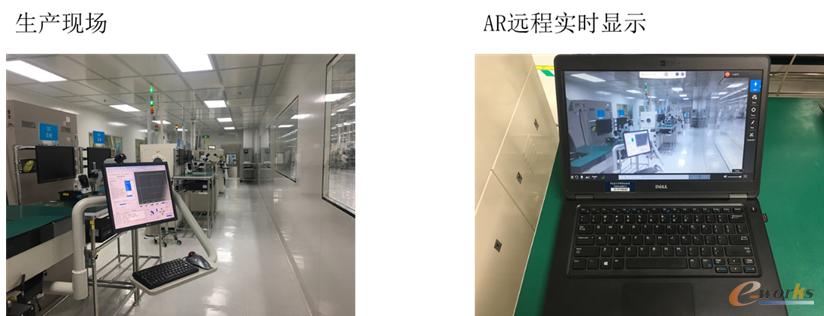
图30 AR虚拟远程诊断示意图
19)车间环境智能管控情况。车间环境(热感、烟感、温度、湿度、有害气体、粉尘等)智能监测、调节、处理系统情况。车间废弃物的产生与排放的计划情况,在信息系统中对废弃物的产生和处理过程进行追溯的情况,废弃物处置是否符合环境保护、安全生产的规定和要求。使用危险化学品、涉重金属等存在较高安全与环境风险的车间是否建立在线应急指挥联动系统。
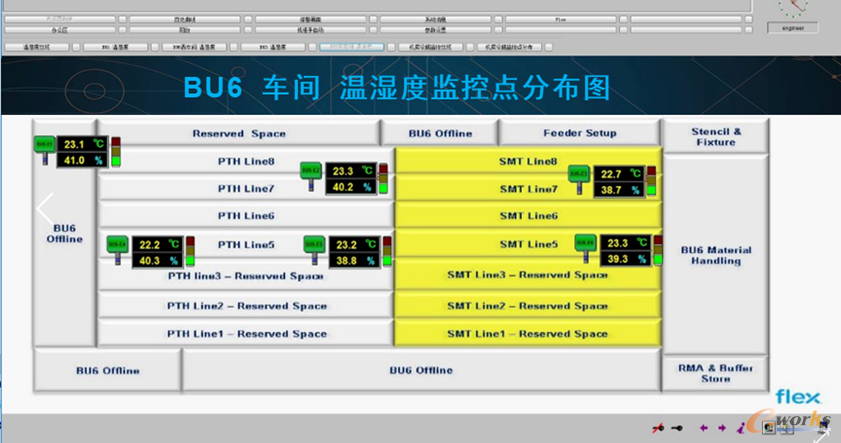
图31 车间温湿度监控布局图
车间总共有18个现场远程监控点,除个别点依据生产要求特别布置,其他大多数监控点都平均分布于车间,以保证车间的各区域温湿度均衡。车间温湿度范围主要依据生产工艺、物料特性的要求以及人员的舒适度来进行设定:如主车间的温湿度要求为18~27℃,30%~60%,个别区域如无尘室为20~25℃,40%~60%。且依据外界季节不同可将控制点进行设定,如主车间在冬季会将温湿度控制点设定于20℃左右和40%左右;夏季会将如主车间在冬季会将温湿度控制点设定于25℃左右和50%左右,以起到节能节电的效果。数据采集为可选,如不需要采集程序,可提供下面采集模块的通讯协议,供测试自行采集。若需要提供采集,与测试程序接口可商定。软件功能可选:实时值显示、实时曲线显示、丰富数据管理功能、报表输出、定时自动备份、记录查询。
20)资源能源消耗智能管控情况。能源综合管理监测系统建立情况,请提供能源综合监测系统架构图、主要功能描述。企业生产与能耗预测模型构建情况及应用效果,生产与能耗预测模型构成及应用效果。重点环节节能优化模型构建情况及应用效果。能源供给、调配、转换、使用等重点环节的节能优化模型构成及应用效果。
电量智能监控系统:对我公司的能源消耗情况进行实时监控,并能在系统中进行能源分析。
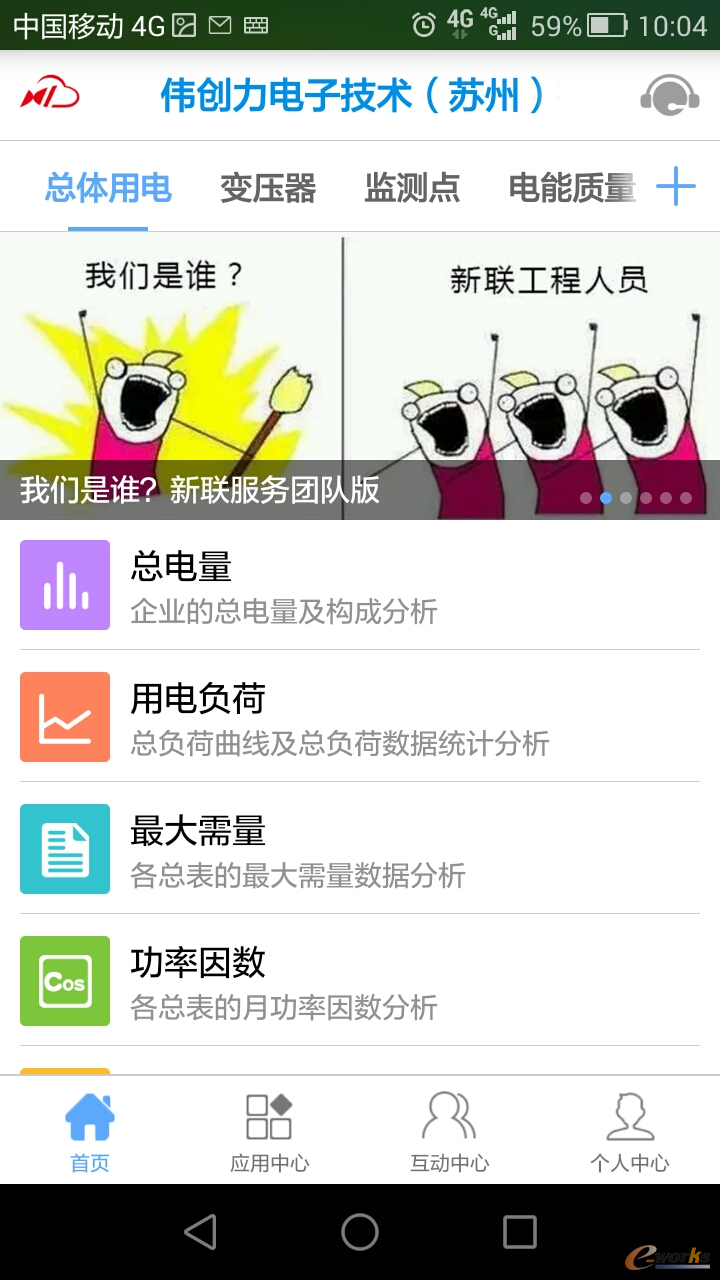
图32 电量智能监控系统APP界面图
21)车间与车间外部联动协同情况。车间与车间外部信息系统联通情况、数据接收反馈情况。车间集成应用计算机辅助设计及仿真系统、制造执行系统(MES)、企业资源计划管理系统(ERP)、分布式控制系统(DCS)等信息与自动化系统情况。
产品数据管理系统(PDM)会收到客户给出的产品设计信息,转换为我们的标准内容后,产品数据管理系统会在有新产品或者产品有更新内容后自动发送给企业资源计划管理系统(ERP),企业资源计划管理系统(ERP)里,在客户下定订单后,会把产品信息,以及工单信息通过自动接口下载到制造执行系统(MES)里面,在制造执行系统里,具体执行工单进行生产时,当产品完成元器件贴打,检验,功能测试,包装等等生产步骤后,制造执行系统(MES)会根据序列号条码跟踪产品状态,在完成相关必须流程后,系统在预定的状态会自动触发产品完成,并把此信息上传到企业资源计划管理系统(ERP),然后企业资源计划管理系统(ERP)会自动根据产品数据增加成品库存同时扣除原材料库存。从车间管理角度,根据产品的流动来把车间内的制造执行系统(MES)和车间外的企业资源计划管理系统(ERP)无缝集成起来,实现高效的联动管理。
在企业内部系统集成运转的情况下,我们建立了企业的大数据仓库,把制造执行系统(MES)数据,生产设备数据,和企业资源计划管理系统(ERP)数据,根据企业情况进行集中,然后根据企业需求对数据进行智能分析主要包括:从前到后的全面质量,产线的利用效率,生产能力以及瓶颈工位分析,产品工程能力分析等等。通过分析,帮助各级企业决策人员找到企业的提高空间,来帮助改善企业的关键能力,比如质量,效率,工程能力等等,从而为企业提高智能化管理能力的同时也带来更好的效益。
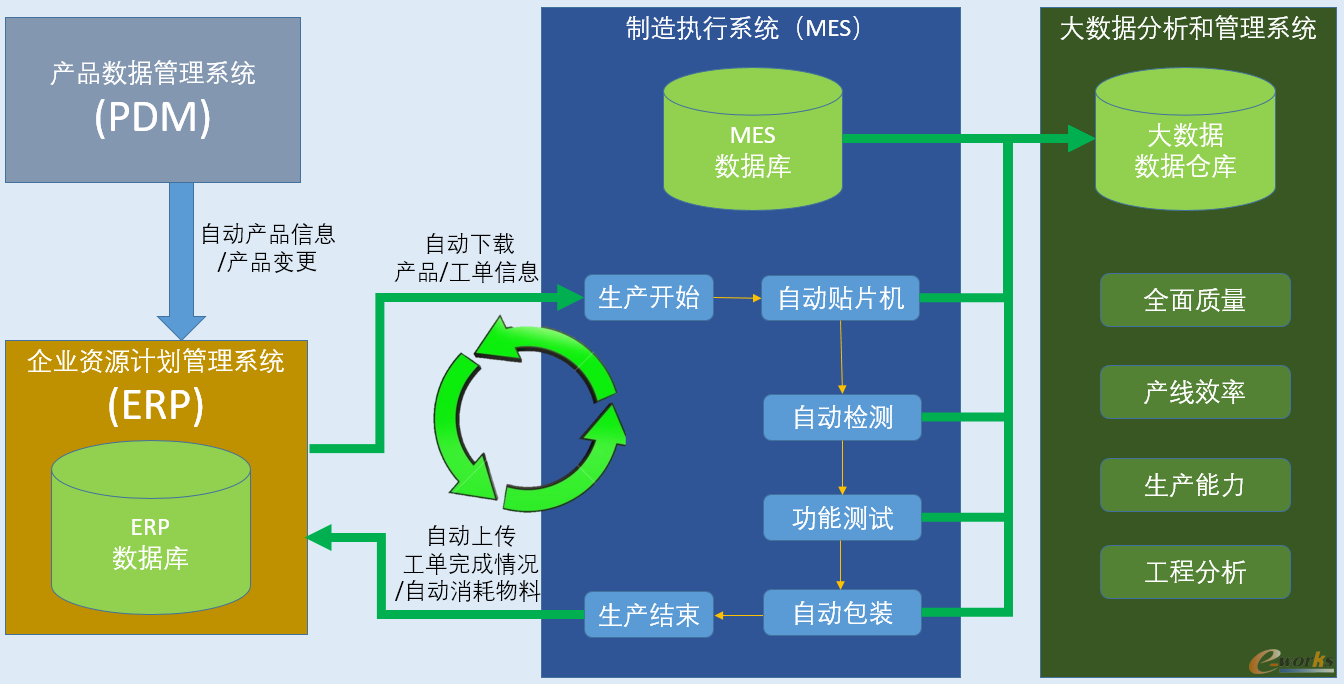
图33 车间与外部联动协同系统集成方案图
3. 效益分析
1)项目产品的实施可以大大地推进通讯互联设备的国产化进程,提升国产通讯互联设备的核心竞争力及市场占有率,推进我国电子信息行业的产业升级,符合 “智能制造” 及中国制造2025发展方向。
2)通过信息化建设,所有的技术人员都通过计算机辅助设计,缩短了产品研发的周期。同时公司通过技术创新,自主研发了Flex Flow生产管理系统,极大的提高了生产能力和产品的合格率。